Catalytic Carbons Help
Remove Chloramine
They succeed where other carbons may fail.
By Steven D.
Spotts
Where chlorine creates high levels
of trihalomethanes (THMs), chloramine can be an alternative for
disinfecting drinking water. Removing it at the point of use (POU),
however, can be more difficult than removing chlorine. When your job
requires chloramine removal, you may consider using catalytic activated
carbons.
Chloramine is more stable than free
chlorine and is thus a much weaker oxidant. As a result, it forms less
THMs. Typical chloramine residual throughout municipal distribution
systems is 1 to 3 parts per million (ppm). It's estimated that 13 percent
of municipalities use chloramine as a disinfectant. This percentage is
increasing as municipalities are faced with tougher standards.
Chloramine can also be created in
water through the reaction of ammonia and residual free chlorine. Ammonia
is most common in surface water and is produced by pesticide runoff and
animal wastes. It's estimated that 5 to 10 percent of water supplies
contains 1 to 3 ppm chloramine from this source.
In potable water, chloramine can
exist as monochloramine, dichloramine and trichloramine. Monochloramine
(NH2Cl) is produced in water where the pH is between 7 and 9.
Because the pH of most water delivered through public water systems ranges
from 6 to 9, monochloramine is the predominant species used for
disinfecting.
Because of its highly stable nature,
monochloramine is also the most difficult type of chloramine to remove
using activated carbon. Dichloramine (NHCl2), a much less
stable compound, is predominant in water when the pH is 4.4 to 6 or at
chloride-to-nitrogen ratios between 5 to 1 and 7.6 to 1. Activated carbon
readily removes dichloramine from water.
Trichloramine (NCl3), or
nitrogen trichloride, occurs only at pH levels of less than 4.4 or at
chloride-to-nitrogen ratios exceeding 7.6 to 1. Because it exists only in
a low-pH environment, it isn't usually a concern for water treatment
professionals.
Potable water with residual
chloramine is considered to be a problem or potential problem to many
industries, as well as a taste and odor concern to many home owners and
commercial establishments.
Laboratory studies show that many
conventional activated carbon products made from a variety of starting
materials have some affinity for monochloramine removal.
Because the chloramine conversion
reaction is catalytic in nature, however, activated carbons that exhibit
enhanced catalytic activity are more efficient (see graph). In theory,
monochloramine removal is a two-step reaction:
(1) NH2CL +
H2O + C* ---> NH3 + H+ Cl-
+ CO*
(2) 2NH2 Cl + CO* --->
N2 + 2H+ + 2Cl- + H2O +
C*
where C* and CO* represent
surface carbons and surface carbon oxides, respectively, which are
active sites for the monochloramine reaction.
It's theorized that chloramine
removal is enhanced with catalytic activated carbons because of their high
number of catalyst sites compared to conventional carbons.
For both conventional and catalytic
carbons, the rate of chloramine removal is initially faster than at steady
state because surface carbon oxides eventually supplant the carbon active
sites and results in a slower removal rate. The period during which this
happens is known as the induction period.
The chloramine removal efficiencies
of catalytic carbons cut required contact time, extend bed life and enable
you to use smaller equipment. Each of these advantages translates into
cost savings for the end user without sacrificing any of the carbon's
capabilities.
Particle size affects catalytic
carbons similar to the way it affects conventional activated carbons.
Although it influences the rate and extent of monochloriamine removal,
this isn't as significant as it is in dechlorinating
applications.
Smaller particle size translates to
greater bed life for a given treatment objective and empty bed contact
time (EBCT), but as particle size decreases pressure drop considerations
increase, resulting in diminishing capacity improvements.
In general, increasing contact time
significantly improves monochloramine removal capacity as well as the
achievable effluent level for all carbons. However, the increased activity
of catalytic carbons makes it possible to use shorter contact times or
smaller equipment. Thus, for existing systems where conventional carbon
has problems removing chloramine, catalytic carbons will show marked
improvement and cost savings.
This concept is particularly
important in POU applications where contact times are on the order of 10
to 30 seconds. In addition, increasing EBCT has a stronger effect on the
efficiency of monochloramine removal by catalytic activated carbons than
it does on conventional carbons.
For example, using the same test
conditions and carbons described in the graphs, changing the EBCT from 10
seconds to 25 seconds improved the performance of the catalytic carbon
threefold. The conventional carbon improved by only 30 percent. Likewise,
increasing EBCT to 50 seconds led to an even more dramatic performance
improvement for catalytic carbons compared to conventional
carbons.
Because of the improved removal
efficiencies of catalytic carbons, bed life can be extended two to four
times longer than can be achieved with conventional activated carbons.
These efficiencies may be further improved through use of extruded or
molded block technologies which capitalize on improved adsorption kinetics
through use of smaller particle sizes.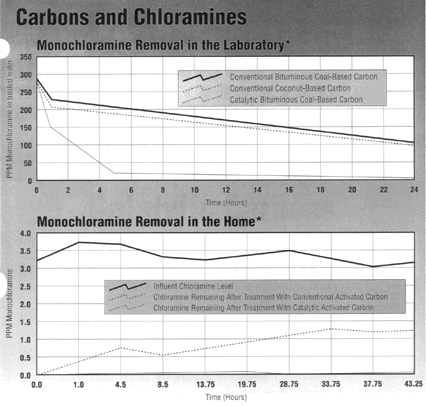
*Conventional carbon shown
features a Peroxide Number (PN) of 60 minutes and an Iodine Number (IN) of
953. Catalytic carbon shown features a PN of 12 minutes and an IN of 930.
Both carbons are 20 x 50 U.S. mesh bituminous coal-based products. In both
cases, 50 cubic centimeters of carbon were tested with deionized,
chlorine-demand-free water at 20 C. Influent contained 3 to 4 parts per
million (ppm) chloramine and 24 ppm alkalinity as CaC03 . Empty
bed contact times were 50 seconds and pH was 8.5. The chloramine treatment
objective was 0.1 ppm.
Catalytic carbons can't remove
monochloramine indefinitely. Adsorbed contaminants tend to occlude
catalytic sites, eventually reducing chloramine removal efficiencies to
the point where thermal reactivation or replacement is necessary. Yet
because most municipal water is relatively low in organic contaminants,
organic competition for adsorption or reaction sites shouldn't be a
significant concern.
Catalytic carbon can remove
chloramine from water more efficiently than conventional activated carbon.
Because catalytic carbons have considerably faster reaction kinetics for
conversion of chloramine, your customers can realize cost savings through
reduced empty bed contact time, extended bed life or by using smaller
equipment. In some chloramine removal applications, catalytic activated
carbons may be used where conventional carbons were
ineffective.
Steve Spotts is marketing manager
for the commercial business group at Calgon Carbon Corp., Pittsburgh,
PA. |