The Blacksburg · Christiansburg · V.P.I. Water
Authority
by Austin Hill Shaw (ashaw@vt.edu) Hee-Chae Lee
(koma@vt.edu)

Behind the potable, palatable water that all of Virginia Tech and the surrounding communities
depends upon daily, is the Blacksburg,
Christiansburg, V.P.I., Water Authority. Established in 1954 and constructed
in 1957, the Water Authority has been treating an average of six to seven
million gallons of water a day. The Water Authority deals solely with drinking
water and is not involved in waste water treatment. Operating 24 hours a day, 7
days a week, the Water Authority runs a lean operation, staffing only 12 people
to run the entire facility. Despite this, using automated and manual methods,
the water is tested on average 249 times a day in and around the plant to ensure
it is fit for consumption. These test can be divided into two broad categories:
test for contaminants and tests for physical parameters. The contaminants
include such things as pesticides, metals, and parasites; substances that can
adversely affect the health of the consumers. The physical parameters, such as
temperature, turbidity, pH, salinity, and odor tests are used to determine the
amount of certain chemicals that will need to be added to successfully treat the
water for the lowest cost possible.
As a water treatment plant, The Blacksburg, Christiansburg, V.P.I. Water
Authority is unique in that it is neither a privately owned treatment system,
nor is it a public municipality. Around the United States, most water treatment
plants fall into one of these two broad categories. Privately owned systems are
required to pay taxes on the water they sell and sometimes must compete with
other privately owned water treatment operations. On the other hand, public
municipalities are sometimes neglected due to their control by elected
officials, who sometimes fail to maintain facilities in face of more politically
charged projects. Walking the line between a private facility and a
municipality, the Water Authority is a tax exempt organization governed by a
representative from each of the three served areas, plus two additional
representatives the three districts agree upon. The Water Authority pays for the
cost of operation by wholesaling their water for $1.06 per thousand gallons to
the three districts and not through tax collection. Thus, the Water Authority
doesn't have to rely on tax revenues because they are wholesaling the water to
cover their operating expenses; they don't have to compete with privatized
treatment plants; they are immune from the deleterious affects of political
cycles and, in addition, the Water Authority maintains the right to condemn
property as needed. As Superintendent Jerry Higgens puts it, "our situation is
ideal."
The Water Treatment Process

The process begins with raw water being pumped out of the New River. The
water is filtered though large screens which prevent large objects from entering
the treatment system and damaging the equipment therein.
The water is analyzed for turbidity and pH automatically so appropriate levels
of chemicals may be added further along in the treatment process.The raw water
is pumped into the flash mix basin, a turbulent well mixed environment. Before
the raw water enters this area it is injected with chlorine gas, sodium
hydroxide, and polyaluminum chloride (PAX). These three chemicals are used for
the sterilization of the water, the adjustment of pH to hinder corrosion in
pipes, and to begin the coagulation process respectively. PAX promotes the
process of coagulation by creating chemical attractions between particles due to
the presence of the aluminum ion in the water. As the name implies, the primary
purpose of the flash mix basin is to distribute the added chemicals evenly
throughout the water.
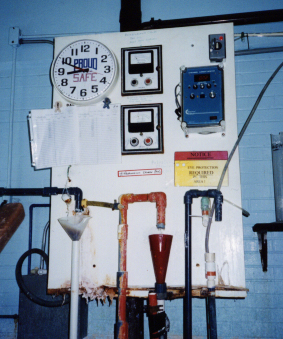 Flash Mix Basin Chemical Feeder(Image)
Next
the water flows into two separate flocculation basins and mixers. The conditions
are far less turbulent but the water remains well stirred. The water remains in
these two separate, but identical treatment paths, until the they converge again
at the clear wells which mark the final stage in the treatment process. In the
flocculation basins and mixers, large low speed paddles stirs the chemically
treated water. Suspended solids in the presence of PAX form larger and larger
clusters of particles, known as flocs, as the water is slowly stirred. As the
flocs grow in size as additional particles latch, they also become heavier,
which is crucial for the next step in the treatment process to be successful.
Settling Basin Animation
The water with its well formed flocks flows from the flocculation basins into
the settling basins, an environment almost devoid of turbulence which is
designed as a plug flow reactor. The water takes a minimum of 3 hours to cross
the settling basin and during that time, the flocs settle out of the water and
collect at the bottom. Twice a year, the basins are drained and using
pressurized water, the flocs at the bottom are pushed out to the settling pond
below the plant. In the settling ponds, water from the settled solids and from
the backwash (described later) is allowed to discharge into the steam. After the
water has left the settling basins, most solids have settled out.
The final step in removing particles takes place in the dual media filters. The
water that has left the settling basins filters through a matrix of anthracite
coal, sand, and gravel. The fine particles that did not settle out in the
previous treatment steps, become trapped in the filter, the smallest particles
being trapped at the interface of the coal and the sand where porosity is at a
minimum. The clean water proceed through the filter to the clear well below.
According to regulations, whenever readings show a turbidity of 0.1 in the water
exiting the dual media filters, or there is a head loss of 6.5 feet, or 100
hours elapses, which ever comes first, the dual media filters must be cleaned.
By forcing clean water from the clear well back up through the filter, the
matrix is disturbed and fine particles are flushed out of the system. This
process is called backwashing.
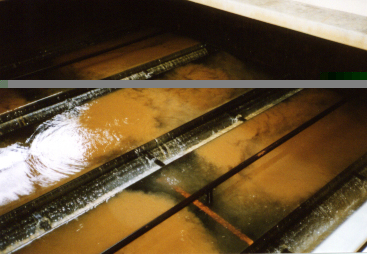 Backwashing in progress
The backwash water with the fine particles in suspension, exits over a baffle
and out to the settling ponds. The matrix is then reestablished simply by
allowing the different sized particles within the matrix to settle back out in
order of there respective densities. In the settling ponds, the solids from both
the settling basins and the backwash are allowed to settle out while the excess
water drains off to the New River.
The final step in the treatment process occurs in the clearwell were the
filtered water is collected and disinfected below the dual media filters. As was
said earlier, the disinfection process really begins at the flash mix basin,
where the entering water is injected with chlorine gas. After settling and
filtration, the water is now almost devoid of suspended particles. But
pathogenic organisms and other organic substances may still remain in the water.
While organics can make the taste and odor of the water undesirable, the
presence of certain pathogens can cause sickness and even death to consumers. In
the clearwells, additional chlorine gas is dissolved into the water. This
dissolved chlorine oxidizes both the pathogens and organics and leaves the
waters safe and desirable to drink. The Water Authority also adds additional
chlorine to protect the water from contamination on its path from the plant to
the consumer.
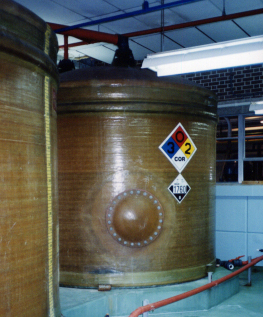 Chemical Storage Tank
Once the water has been disinfected in the clearwell, it is suitable for
consumption. However, to inhibit the corrosion process in the pipes of the
communities, pH is adjusted if need be using sodium hydroxide to make the water
slightly basic. In addition, as water leaves the clearwell, zinc orthophosphate
is added to further retard corrosion. The finished water then makes its way
through a series of pumps, pipes and reservoirs to storage tanks in the three
surrounding communities. The water in the distribution system is under pressure
so that opening any tap in the community will yield safe, pleasant water for
consumption.
Acknowledgements
The majority of the
information for this web page was gathered during an interview with the Water
Authority's superintendent, Jerry Higgens. The interview and tour of the plant
took place on Thursday, October 16, 1997. Additional information was gathered
via telephone conversations with Jerry Higgens and various employees of the
plant. The authors of this web page would like thank Jerry Higgens and all those
at the Water Authority who helped to make this web page possible.
Send comments or suggestions to: Student Authors: Austin Hill Shaw and
Hee-Chae Lee Faculty Advisor: Daniel Gallagher, dang@vt.edu Copyright © 1997 Daniel
Gallagher Last Modified: 2-14-1998 |